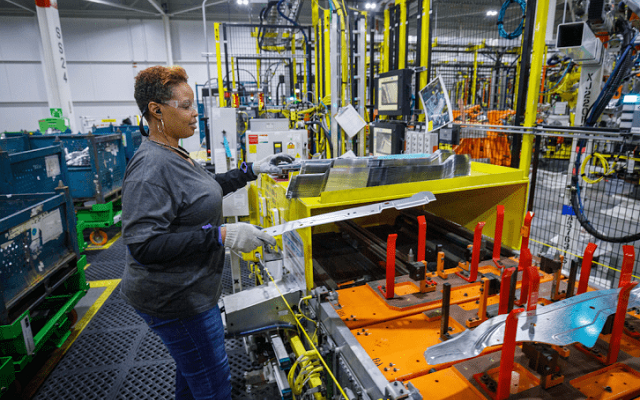
The definition of vehicle quality has evolved
J.D. Power process improvement consulting engagements are designed to improve a client’s marketplace performance and resultant financial success. The technique to achieving this can be directly correlated to ensuring the product is correctly and consistently assembled to customer satisfaction target requirements – in a more coordinated, accurate, timely and cost effective manner.
J.D. Power offers a series of highly-effective process improvement solutions:
Assessments
Assessments provide access to J.D. Power’s global manufacturing consulting experts to help identify and recommend the implementation of specific action items that will drive overall quality improvement.
Operations Improvement Support
J.D. Power’s Operations Improvement Support activities are designed to assist clients in addressing opportunities for improvement in order to fuel progress toward an ideal state vision.
Training / Skills Enhancement
J.D. Power offers customized training programs that teach the need to integrate the Voice of the Customer into daily work activities to help improve the quality of the overall output.
Assessments
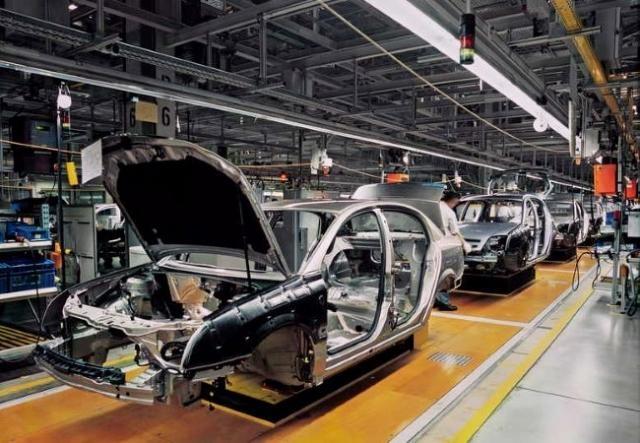
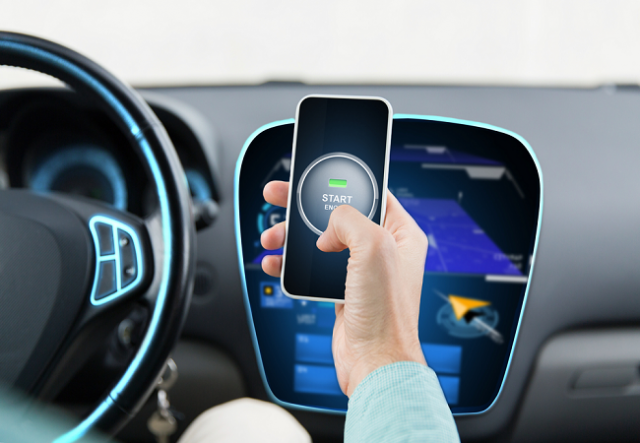
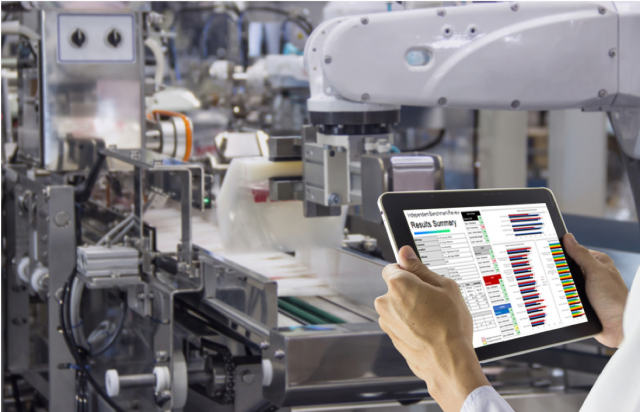
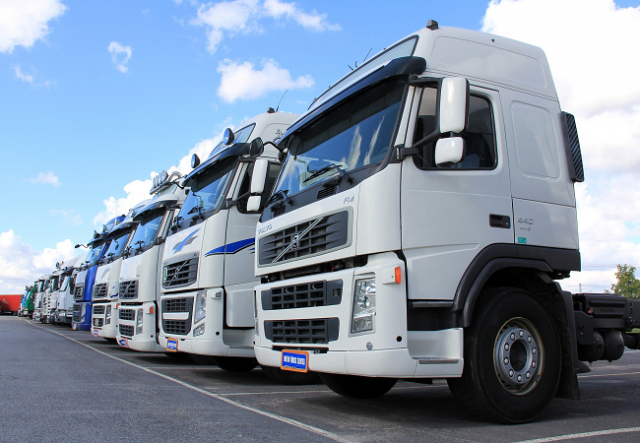
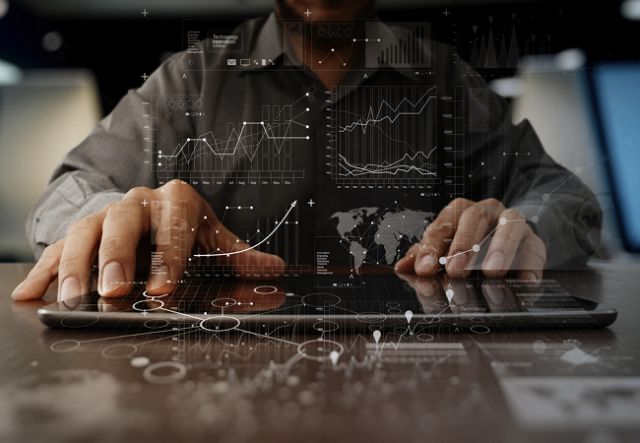
Process Improvement
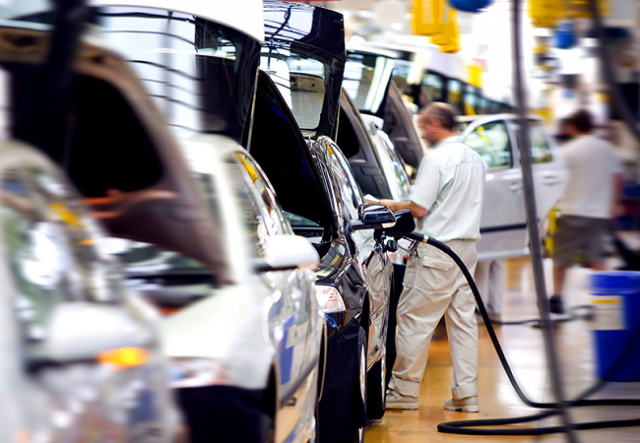
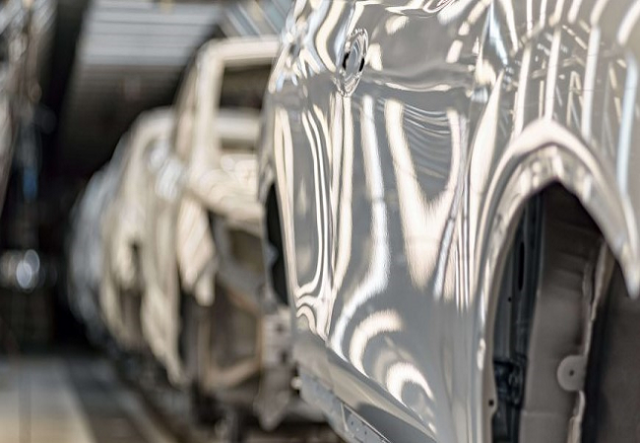
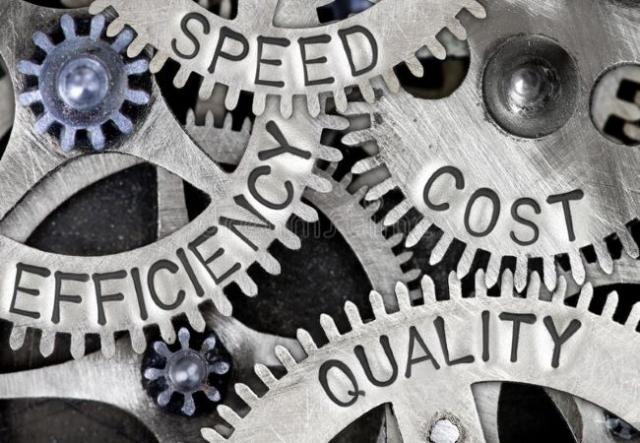
Training / Skills Enhancement
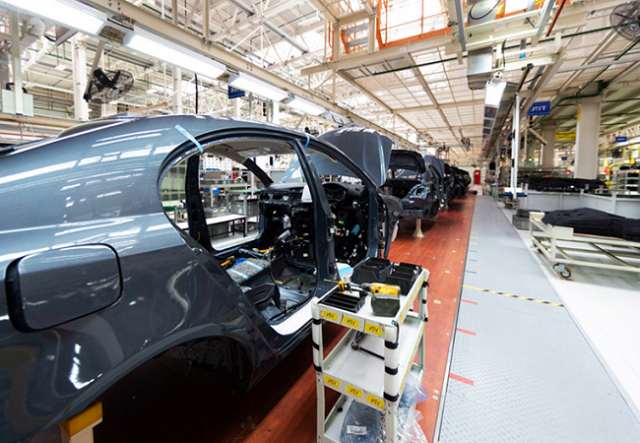
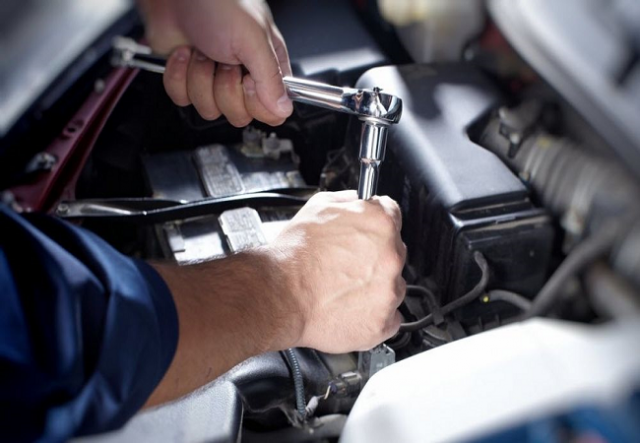